Technology has advanced a lot since the second half of the 20th century developed computers as we know them today. The process of miniaturization of components forces us at every step to want to make things smaller and smaller, and this has been the case for all electronic components except one: the battery. While it is true that batteries have received major improvements and have appeared in new classes and can be made of various voltages, the improvements are minuscule compared to the advances that have taken place in microprocessors or displays, to name two basic examples.
It is for this reason that there are many companies and R&D groups striving to improve battery operating technology. If I want to present to you today, the protagonist is LG Chem (also known as LG Chemical), a subsidiary of the LG group, as it has taken a huge step forward in how to power a device.
In their work published in Advanced Materials just over a month ago they describe the manufacture and operation of a flexible, cable-shaped battery based on lithium-ion. Current batteries are something static that cannot bend or undergo large deformations, so the appearance of this new type of battery would open the doors to a whole new generation of devices that take advantage of these advantages.
Two direct consequences would be that batteries would no longer have to be placed inside laptops, tablets, or phones so that I could make them much thinner. And what would be much more interesting: completely original designs of new devices could appear in the minds of industrial designers than we know today. Can you already think of a new product?
A) Sidecut to see the different layers. B) Cross-section to see the inside of the battery.
Battery structure
The elements of which we made the cable are well-differentiated and each one performs its function. Taking a tour from the inside out we have:
A) Stable alloy with 5.5% nickel.
B) Alloy fractured with 23.9% nickel.
Hollow helix of copper cables covered with a tin-nickel alloy. It has a total diameter of 1.2 mm and is in the innermost part of the cable, to act as an anode for the battery. The helix is hollow to facilitate movement and allow the cable to bend. Someone carefully chose the alloy since Ni-Sn alloys allow an acceptable capacity and sufficient endurance to withstand a good number of cycles. This in theory is very simple, but the choice of the correct proportion to work with complicates the matter a lot. Based on tests, the researchers determined that the ideal proportion was one containing only about 5% nickel. The higher the concentration of nickel, the greater the number of cycles supported, but the flexibility decreases and the material becomes more fragile when minor breaks occur, as we can see in the image (B) that accompanies these lines. We must reach a compromise between flexibility and the number of cycles.
A polyethylene ( PET) separator is changed to withstand temperatures of more than 100ºC that occur during the manufacturing process. Its function is simply to separate the hollow interior of the cable from the outer layers. Its thickness is only 50 cm.
200 μm diameter aluminum cable. Coiled over the separator is this aluminum cable whose function is that of a cathode current collector, it serves as a positive terminal. The copper wires from the anode make up the negative terminal.
Lithium compound. It is a LiCoO 2 sheet that surrounds the inner layers and acts as the cathode of the battery. Its thickness can be between 100 and 150 cm. This variable, together with the number of cables that make up the helical anode, is what determines the electrical storage capacity of the battery.
Finally, an insulator is placed that packs the entire battery and protects it from the outside. They are tubes made of a material that responds to heat so that when the temperature is applied, it contracts, exerting a dominant force. In this way, the battery is pressed and is well protected from the outside. The thickness can be of the order of 300 cm.
Although this is the entire structure of the battery, its components do not end there. A final element is necessary: the electrolyte. A liquid containing lithium hexafluorophosphate ( LiPF 6 ), a compound commonly used in lithium batteries, is injected into the hollow area created by the helical structure of the anode. This electrolyte will provide the free ions necessary to convert the medium into a conductor of electricity, thus allowing the battery to function properly.
Functioning
The key element in this new battery is the splendid arrangement of the cables that make up the internal helix (anode). Its studied design allows the cable to be completely flexible and to avoid operating problems. Thanks to its arrangement and the existing gap inside, bending the cable does not produce any of the three basic problems that lead to errors when current batteries are deformed: component displacement, contact breakage, and the creation of short circuits. However, this is not the only advantage, but the studies carried out also show a greatly improved battery capacity and allow the charging and discharging processes to be much smoother.
Optical and scanning microscope images (lower inset) of the helical hollow anode.
To objectively and precisely study the operating conditions of the battery in simultaneous stress and discharge experiment, I used a device that produced a small deformation every 20 minutes. Thus, by continuously measuring the capacity of the battery from its initial 4 V, it was verified that the discharge of the battery did not vary when the cable was bent. Only on one occasion was there a small jump of only 0.03 V, which is not an impediment to affirm that the operation is perfectly stable under mechanical stress.
The next steps will be to study the performance of the battery against cyclical efforts, as well as fatigue, to know how long it lasts operating under optimal conditions. Obviously, many safety studies will also be necessary to show that its use is suitable in future devices that want to make use of this technology. At the moment the tests carried out are very positive: they have been able to illuminate an LED screen continuously despite making a thousand and one tricks to the cable, and to power an iPod Shuffle by placing two pairs of cables in series, two connected to two in parallel.
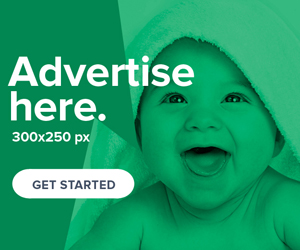